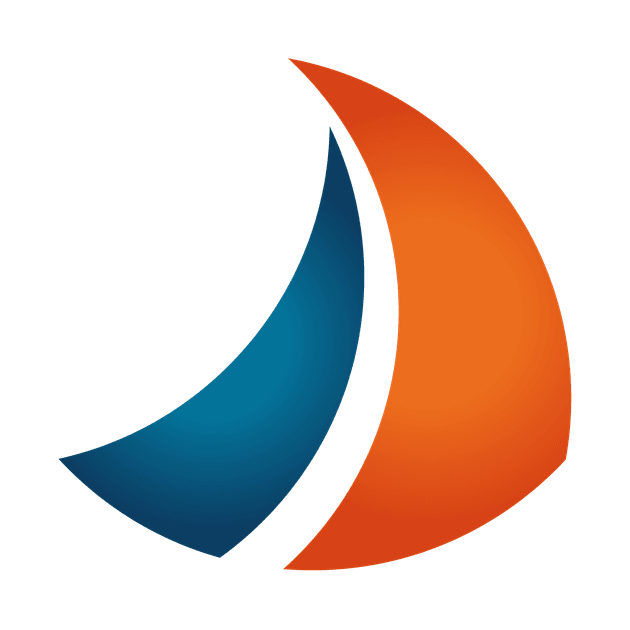
“In the past, we used to access payment data manually on a daily basis, but now we don't have to.”
- Hajnalka Berbás, CFO
Komlói Fűtőerőmű Zrt.
More accurate data, faster processes, more efficient work
The Komló Heating Power Station has always had the strategic goal of providing high quality service to its customers, both in terms of its district heating activities and customer service.
In 2021, the company recognised that the IT systems it was using did not meet the requirements of the digital age, that the state of system security posed operational risks, and that the lack of data connectivity and the level of manual work had led to a loss of operational efficiency. In addition, it was extremely difficult to maintain the basic infrastructure and operations in terms of hardware and printers due to the technological obsolescence of the previous management system, which was no longer compatible with the equipment currently available.
Another problem to be solved
Another issue was the way the data was stored during database operations, which resulted in the complete loss of historical data during a meter change. The lack of parallelisation functionality was also a barrier to smooth operation, often causing significant slowdowns and system lock-ups when processing large volumes of invoices.
These findings led to a major decision to replace the existing invoicing system and to implement an integrated ERP system with technical records and online data connectivity.
The solution
To solve the identified problems, they selected the solution of AppVision Ltd., who proposed an integrated ERP system that covers the entire spectrum of business management, from finance and accounting to inventory management and service activities, providing advanced support for the district heating provider's billing, collection, receivables management and customer service processes. In addition, it provides a real-time data link to the existing online customer support site of the Komló heating power utility.
The solution is based on the Microsoft Dynamics 365 Business Central enterprise management system, complemented by a district heating industry solution developed by AppVision Ltd. Running in the cloud (online), Business Central did not require the maintenance of locally installed and operated servers, so it could be cost-effectively integrated into the existing IT environment. The Business Central system is hosted and continuously updated directly by Microsoft, guaranteeing security, high availability and compliance with the current regulatory environment.Another key element of the solution is the district heating industry application developed by AppVision Ltd., which was created specifically to support the business processes of district heating suppliers. The extension is available through Microsoft's AppSource marketplace, and its functionality includes energy, metering data processing, bulk and individual billing, group and postal collection, as well as support for customer service and claims management.
The process
The preparation and implementation took more than a year, and one of the biggest challenges was to cleanse the nearly 30-year-old database and adapt it to the new system. Data migration was done in several steps, with check runs after each step to ensure data consistency. Before going live, parallel billing was performed with the uploaded data, which helped to reduce the billing discrepancies between the two systems due to data errors.
Maintaining the existing and well-functioning customer service portal was a key objective during the implementation. The existing file-based, once-daily update frequency data connection with the previous billing system was replaced by a real-time, machine-to-machine connection. This connection allows the data of issued invoices and online payments to be displayed to end users in real time.
During the implementation process, it was discovered that the meter data file contained outdated and inconsistent data. This discovery led to the installation of a large number of remote-readable water meters in the network as part of a meter replacement programme. This required the establishment of an automatic data link with Techem's data reporting system. The metering data collected can now be imported into the corporate management system in one step.
The many new features have tested both the implementation team and the end-users of the system, so there are still areas of work to be done after the go-live. These include service and maintenance activities, the development of mobile device-supported barcode warehouse management, and the digitisation of some processes that are currently paper-based.
Results and vision
Komló Heating Power Station has been using the system since January 2024, and the positive change is noticeable in several areas.
The most striking result is that processes have been significantly accelerated, and colleagues are able to handle multiple tasks simultaneously. As a result, long waits during the day and the need to work outside working hours or at night have been eliminated.
Thanks to the migration, financial data is now up-to-date and automated, including bank account management, invoicing and payment information.
The automations put in place will greatly help to increase the efficiency and accuracy of workflows.
The meter replacement project has speeded up the billing preparation process and is expected to increase the accuracy of water metering for hot water services, thereby reducing losses in the mediated service. This not only optimises technical processes, but also contributes to improving customer relations, as the flow of information has become faster and more transparent.
Registration for online customer service has been made easier thanks to the real-time data connection between the customer service portal and the ERP system.
In addition, the system implemented guarantees the integrity of historical data files, protecting against incorrect clock data reporting by customers, eliminating losses associated with inconsistent clocks. As a further result, the implementation of the system has inspired the technical team to connect the heat exchanges to the remote monitoring system, taking another step towards improving the quality of district heating services.
Address
1087 Budapest, Könyves Kálmán krt. 48-52.